You are here :
Control System Design - Index | Book Contents |
Chapter 2
| Section 2.5
2. Introduction to the Principles of Feedback
2.5 Prototype Solution to the Control Problem via Inversion
One particularly simple, yet insightful way of thinking about control
problems is via inversion. To describe this idea we argue as follows:
- say that we know what effect an action at the input of a system
produces at the output, and
- say that we have a desired behavior for the system
output; then one simply
needs to invert the relationship between input and
output to determine what input action is necessary to achieve the
desired output behavior.
In spite of the apparent naivety of this argument, its embellished
ramifications play a profound role in control-system design. In
particular, most of the real-world difficulties in control relate
to the search for a strategy that captures the intent of the above
inversion idea, while respecting a myriad of other considerations,
such as insensitivity to model errors, disturbances, and
measurement noise.
To be more specific, let us assume that the required behavior is
specified by a scalar target signal or
reference r(t),
that has an additive disturbance d(t).
Say we also have available a single manipulated variable, u(t).
We denote by y(t) a function of time:
.
In describing the prototype solution to the control problem below,
we will make a rather general development that, in principle, can
apply to general nonlinear dynamical systems. In particular, we
will use a function,
,
to denote an
operator mapping one function space to another.
So as to allow this general interpretation, we introduce the
following notation:
The symbol y (without brackets) will denote an element of a function
space:
.
An
operator,
,
will then represent a mapping from a
function space, say ,
onto .
What we suggest is that the reader, on a first reading, simply
interpret f as a static linear gain linking one real
number, the input u to another real number, the output y.
On a subsequent reading, the more general interpretation, using nonlinear
dynamic operators, can be used.
Let us also assume (for the sake of argument) that the
output is related to the input by a known functional
relationship of the form
 |
(2.5.1) |
where fis a transformation or mapping
(possibly dynamic) that describes the
input-output relations in the plant.1
We call a relationship of the type
given in (2.5.1) a model.
The control problem then requires us to find a way to generate y=r.
In the spirit of inversion, a direct,
although somewhat naive, approach to obtain a solution would thus
be to set
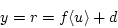 |
(2.5.2) |
from which we could derive a control law,
by solving for u.
This leads to
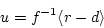 |
(2.5.3) |
This idea is illustrated in Figure 2.6.
Figure 2.6:
Conceptual controller
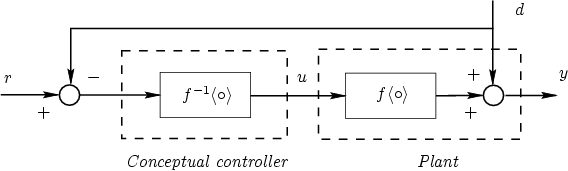 |
This is a conceptual solution to the problem. However, a little
thought indicates that the answer given in (2.5.3)
presupposes certain stringent requirements for its success. For
example, inspection of equations (2.5.1) and (2.5.3)
suggests the following requirements:
|
R1 |
The transformation f clearly
needs to describe the plant exactly. |
|
R2 |
The transformation f should be well-formulated in the sense that
a bounded output is produced when u is
bounded--we then say that the transformation
is stable. |
|
R3 |
The inverse f-1
should also be well-formulated in the
sense used in R2. |
|
R4 |
The disturbance needs to be
measurable, so that u is computable. |
|
R5 |
The resulting action u should be realizable and
should not violate any constraint. |
Of course, these are very demanding requirements. Thus, a significant
part of Automatic Control theory deals with the issue of how to change
the control architecture so that inversion is achieved but in a more
robust fashion and so that the stringent requirements set out above can be relaxed.
To illustrate the meaning of these requirements in practice, we
briefly review a number of situations.
Example 2.1 (Heat exchanger)
Consider the problem of a heat exchanger in which water is to be
heated by steam having a fixed temperature. The plant output is
the water temperature at the exchanger output and the manipulated
variable is the air pressure (3 to 15 [psig]) driving a
pneumatic valve that regulates the amount of steam feeding the
exchanger.
In the solution of the associated control problem, the following issues should be considered:
- Pure time delays might be a significant factor, because this plant
involves mass and energy transportation. However a little thought indicates that
a pure time delay does not
have a realizable inverse (otherwise we could predict the future), and hence R3
will not be met.
- It can easily happen that, for a given reference input, the
control
law (2.5.3)
leads to a manipulated variable outside the allowable input range (3 to 15 [psig] in
this example). This will
lead to saturation in the plant input.
Condition R5 will then not be met.
Example 2.2 (Flotation in mineral
processing)
In copper processing, one crucial stage is the flotation process.
In this process, the mineral pulp (water and ground mineral) is
continuously fed to a set of agitated containers where chemicals
are added to separate (by flotation) the particles with high
copper concentration. From a control point of view, the goal is to
determine the appropriate addition of chemicals and the level of
agitation to achieve maximal separation.
Characteristics of this problem are as follows:
- The process is complex (physically distributed, time varying,
highly nonlinear, multivariable, and so on) and hence it is difficult
to obtain an accurate model for it. Thus, R1 is hard to
satisfy.
- One of the most significant disturbances in this process is the
size of the mineral particles in the pulp. This disturbance is
actually the output of a previous stage (grinding). To apply a
control law derived from (2.5.3), one would need to measure the
size of all these particles or (at least) to obtain some average
measure of this. Thus, condition R4 is hard to satisfy.
- Pure time delays are also present in this process, and thus
condition R3 cannot be satisfied.
One could imagine various other practical cases where one or more
of the requirements listed above cannot be satisfied. Thus, the
only sensible way to proceed is to accept that there will
inevitably be intrinsic limitations and to pursue the solution
within those limitations. With this in mind, we will impose
constraints that will allow us to solve the problem subject to the
limitations that the physical set-up imposes. The most commonly
used constraints are as follows:
|
L1 |
to restrict attention to those
problems where the prescribed behavior (reference signals) belong
to restricted classes and where the desired behavior is achieved only
asymptotically; |
|
L2 |
To seek approximate inverses. |
In summary, we can conclude the following:
In principle, all controllers implicitly generate an inverse of
the process, in sofar as this is feasible. Controllers differ with
respect to the mechanism used to generate the required
approximate inverse. |
1 We introduce this term here loosely. A
more rigorous treatment will be deferred to Chapter 19.
|